lavorazioni
Fresatura
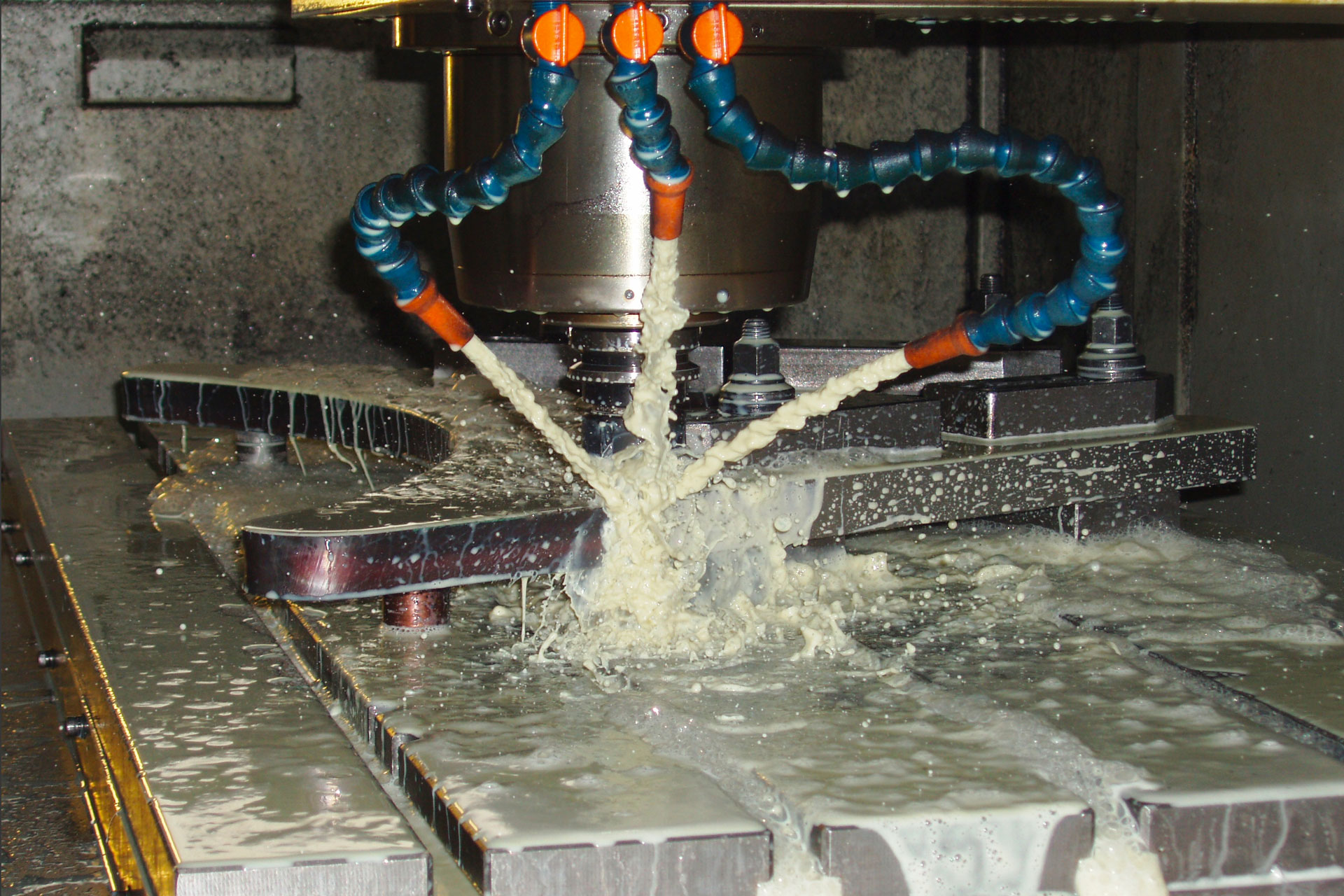
La fresatura è una lavorazione meccanica a freddo per asportazione di truciolo, che permette di realizzare un pezzo finito, la cui forma è stata definita a progetto, partendo da un pezzo grezzo di metallo e asportando il materiale in eccesso, che è detto sovrametallo. Per poter realizzare il pezzo finito è necessario che questo possa essere inscritto nel pezzo di partenza da cui verrà asportato il sovrametallo.
La lavorazione viene effettuata mediante utensili detti Frese, montate su macchine utensili quali fresatrici o fresalesatrici.
La fresatura, a differenza di altre lavorazioni più semplici, richiede la rotazione dell’utensile e la traslazione del pezzo: i taglienti della fresa, ruotando, asportano metallo dal pezzo quando questo viene a trovarsi in interferenza con la fresa a causa della traslazione del banco su cui il pezzo è ancorato.
Il ciclo lavorativo prevede normalmente una prima fase di sgrossatura, in cui l’asportazione viene fatta nel modo più rapido e quindi più economico possibile, lasciando un sufficiente sovrametallo per la successiva fase di finitura in cui si asportano le ultime parti eccedenti per raggiungere le dimensioni previste ottenendo una superficie più liscia. La finitura, che consiste in una asportazione limitata di metallo, consente di rispettare il progetto per quanto riguarda le tolleranze delle dimensioni e il grado di rugosità delle superfici.
Fresatura tradizionale
Nella sua forma più semplice una fresatrice non è altro che un motore, solitamente piuttosto potente, su cui è fissato, tramite un mandrino, un utensile dotato di bordi taglienti (fresa) che ruotano sull’asse della punta stessa. Il principio è lo stesso del trapano, ma le frese sono progettate per svolgere l’azione di taglio sul lato dell’utensile invece che sulla punta, quindi erodendo il materiale invece che forandolo.
Le nostre lavorazioni su fresatrici tradizionali comprendono:
- Singolo pezzo
- Campionatura
Fresatura a controllo numerico
Le fresatrici possono essere controllate manualmente o con sistemi computerizzati: in questo caso la macchina viene definita “a controllo numerico”, o “CNC” (“computer numerical control”).
Le fresatrici CNC più moderne sono dotate di sistemi automatici per la sostituzione degli utensili, in grado di rendere interamente automatizzato il processo produttivo: questo permette, partendo dal materiale grezzo, di arrivare ad un pezzo finito anche senza intervento umano, rendendo le lavorazioni più veloci ed economiche.
Le nostre lavorazioni su fresatrici a controllo numerico comprendono:
- Copiatura
- Profili
- Produzione piccole serie
Tornitura
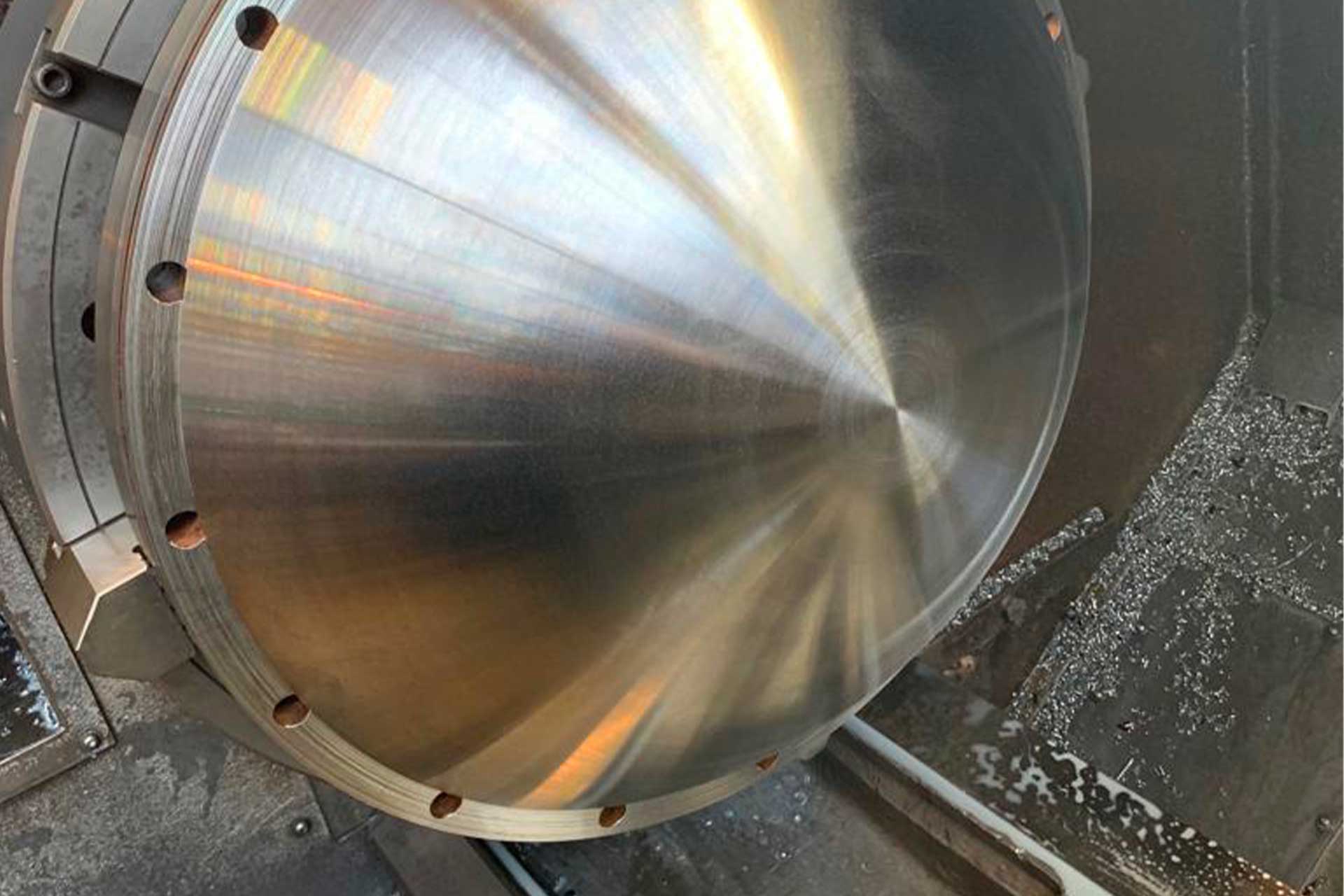
La tornitura è un processo di produzione industriale ottenuta per asportazione di truciolo. La tornitura viene definita da un moto rotatorio del pezzo e un moto per lo più rettilineo dell’utensile (nella fresatura e nella foratura l’utensile possiede invece un moto rotatorio). Il tagliente dell’utensile penetra nel materiale del pezzo e ne stacca la parte in eccesso (sovrametallo) formando così un truciolo. La macchina utensile usata per la tornitura è il tornio.
La tornitura viene utilizzata ampiamente nella lavorazione di metalli, ma anche per legno e pietra. Gli aspetti descritti nel seguito si riferiscono soprattutto alla realizzazione di pezzi in metallo.
Tornitura tradizionale
Il tornio parallelo tradizionale è una macchina utensile molto usata nell’ambito dell’industria meccanica. Esso genera solidi di rivoluzione ed è impiegato soprattutto per la lavorazione dei metalli.
È caratterizzato dal fatto che il moto di lavoro è costituito dalla rotazione del pezzo in lavorazione, mentre l’utensile, solidamente montato su una torretta, scorre parallelamente all’asse di rotazione.
Il pezzo può essere montato a sbalzo su un mandrino autocentrante che sporge dalla testa motrice oppure essere sostenuto tra il mandrino e la contropunta, situata in asse di fronte al mandrino a distanza regolabile. Quando il pezzo è montato a sbalzo è possibile lavorarlo di piatto (tornitura piana), facendo scorrere l’utensile in senso radiale rispetto all’asse di rotazione.
Il tornio parallelo consente essenzialmente lavorazioni basate su simmetrie rotazionali: cilindri, coni, sferoidi, solidi di rivoluzione con generatrice a sagoma.
Tornitura a controllo numerico
Detto anche Tornio CNC (acronimo dell’inglese Computer Numerical Control), rappresenta in un certo senso la massima evoluzione della macchina utensile della quale stiamo parlando.
Può fare tutto ciò che fanno gli altri tipi di tornio, ma tutto avviene in un totale automatismo controllato da un computer. I parametri del pezzo desiderato vengono inseriti in un apposito programma e gli elementi della macchina si muovono comandati dal computer al quale, contemporaneamente alla lavorazione, giungono i segnali provenienti da vari sensori (laser) posti nei punti essenziali così da poter tenere costantemente d’occhio il buon andamento del lavoro.
Se per qualsiasi ragione (ad esempio la consunzione dell’utensile) il sensore registra che il pezzo non rientra più nelle dimensioni impostate vi è un sistema che immediatamente provvede alla necessaria correzione.
La precisione dei pezzi ottenuti con questa macchina è elevatissima, dell’ordine dei centesimi o addirittura millesimi di millimetro. In questo caso l’operatore si limita al controllo dei dati mostrati dal computer ed eventualmente al controllo dei prodotti a campionamento.
ME.TA. ha a disposizione:
- Tornio CNC a 3 assi con teste motorizzate
- Tornio CNC con caricatore di barre
Rettifica
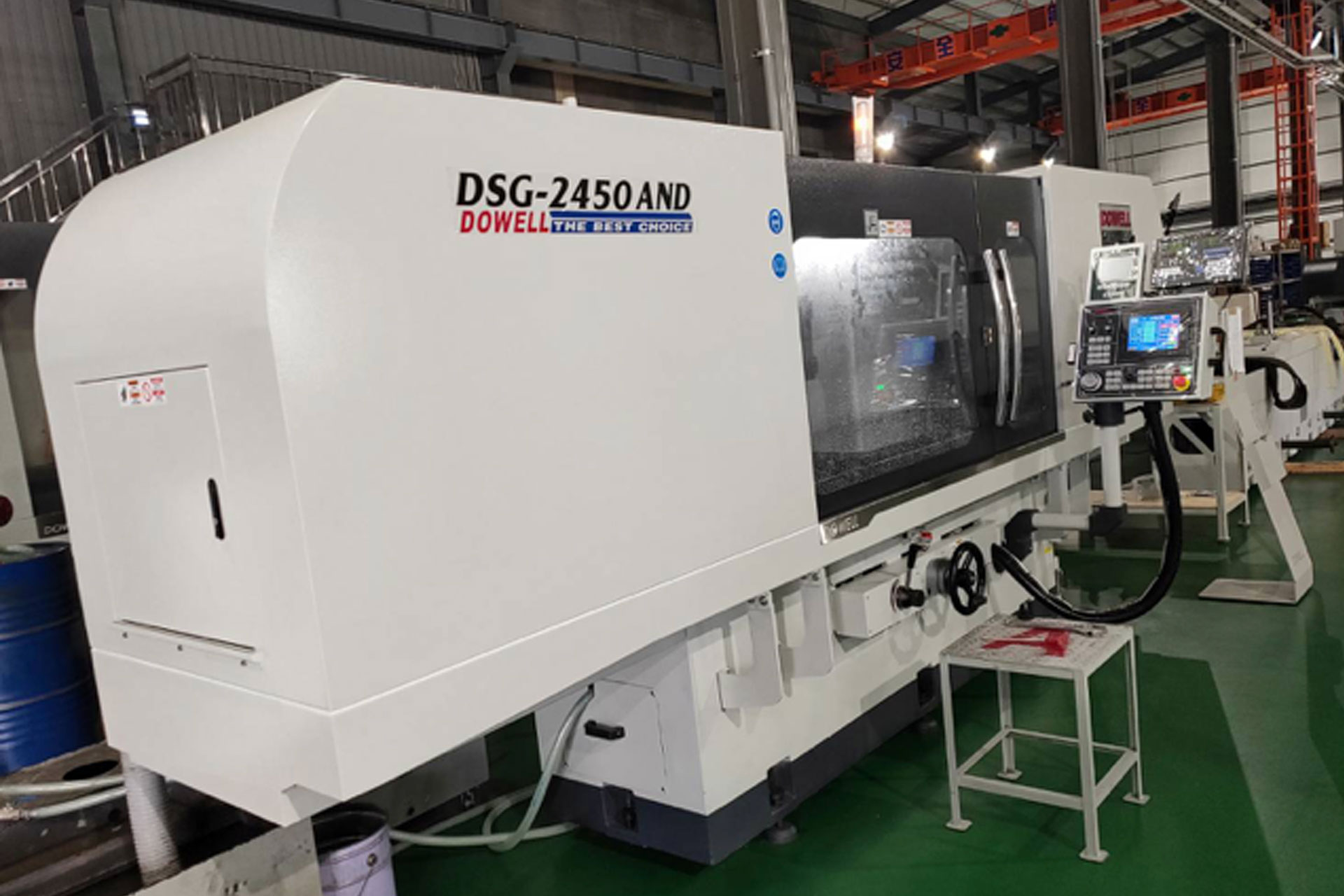
La rettifica è quella procedura eseguita con una macchina chiamata rettificatrice, che ha come utensile una mola a grana fine ed estremamente dura.
La rettifica serve per portare un qualsiasi componente nello stato di forma o superficie ottimale di progetto; questa operazione segue infatti la sgrossatura. Mentre la sgrossatura toglie il grosso dei residui, la rettifica fa sì che tutti i residui o il materiale in eccesso vengano eliminati garantendo alla superficie lavorata un alto grado di finitura.
Rettifica tangenziale
Nella rettifica tangenziale l’albero portamola è parallelo al piano che viene lavorato dalla superficie cilindrica della mola.
Le nostre lavorazioni arrivano fino a 500×1000 e abbiamo a disposizione rettificatrici:
- Semi-automatiche
- Manuali
Saldatura
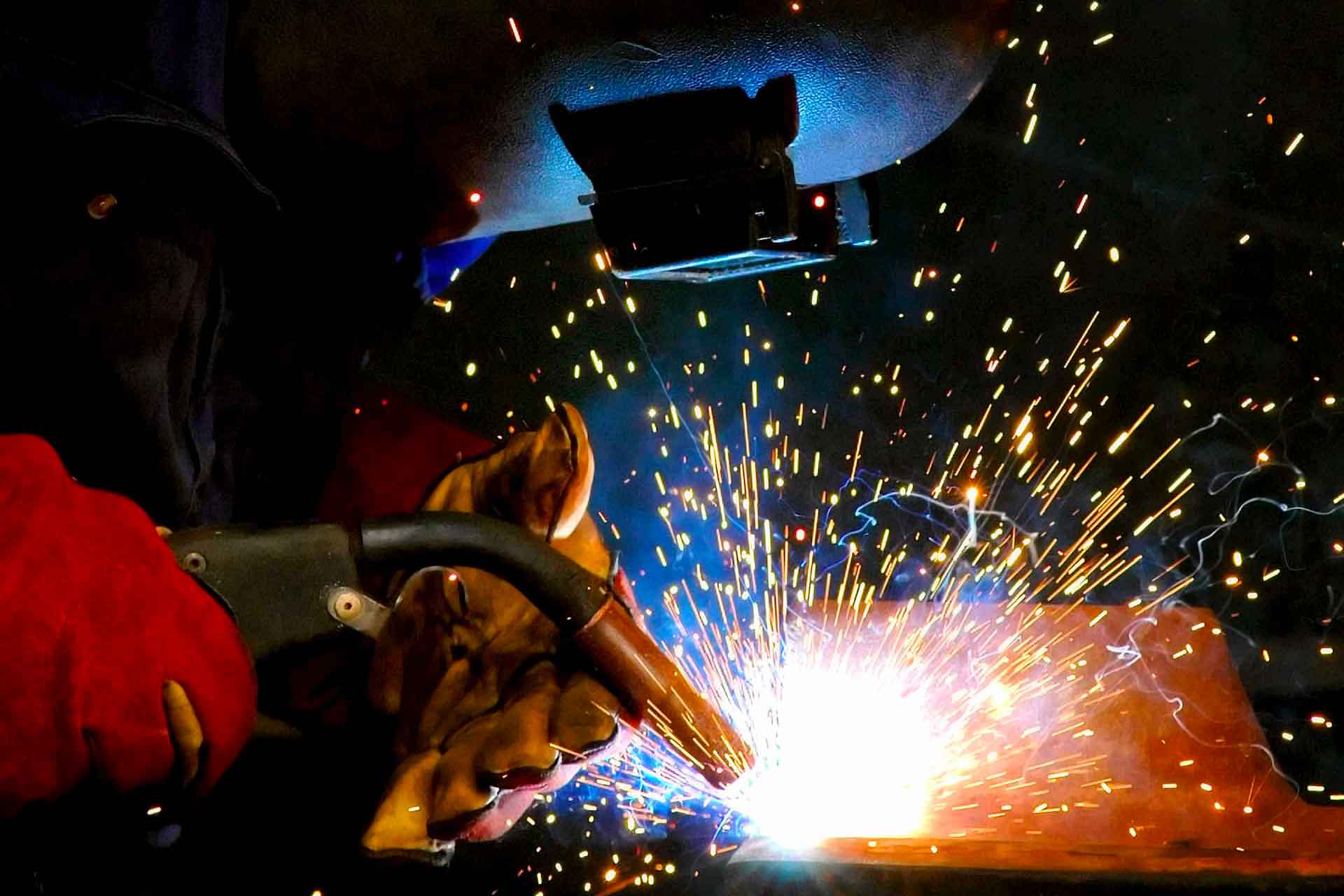
La saldatura è un procedimento che permette il collegamento permanente di parti solide tra loro e che realizza la continuità del materiale ove essa venga applicata.
La saldatura nella sua accezione più comune presuppone l’apporto di calore localizzato tale da permettere la fusione del materiale. Tale materiale può essere il materiale componente le parti stesse che vengono unite, ma può essere anche un materiale estraneo ad esse, detto materiale di apporto: nel primo caso si parla di saldatura autogena nel secondo di saldatura eterogena o brasatura.
La saldatura realizza un collegamento permanente che si differenzia da altri collegamenti permanenti (ad esempio chiodatura o incollatura) che non realizzano la continuità del materiale.
Con alcuni processi di saldatura autogena, qualora eseguita correttamente e secondo certi principi, viene garantita anche una continuità quasi totale nelle caratteristiche stesse del materiale delle parti unite.
Saldatura a TIG
La saldatura TIG (Tungsten Inert Gas) , secondo la terminologia AWS, è un procedimento di saldatura ad arco con elettrodo infusibile (di tungsteno), sotto protezione di gas inerte, che può essere eseguito con o senza metallo di apporto.
La saldatura TIG è uno dei metodi più diffusi, fornisce giunti di elevata qualità, ma richiede operatori altamente specializzati. Questa tecnologia di saldatura fu sviluppata inizialmente per l’industria aeronautica nel corso della Seconda guerra mondiale per sostituire sugli aerei i rivetti con saldature molto più leggere a parità di resistenza.
Meta realizza saldature a TIG con riporti idonei di materiali, anche su temprato e filo continuo.
MONTAGGI
- Attrezzature
- Assemblaggio complessivi
- Dalla costruzione al montaggio.
Collaudo
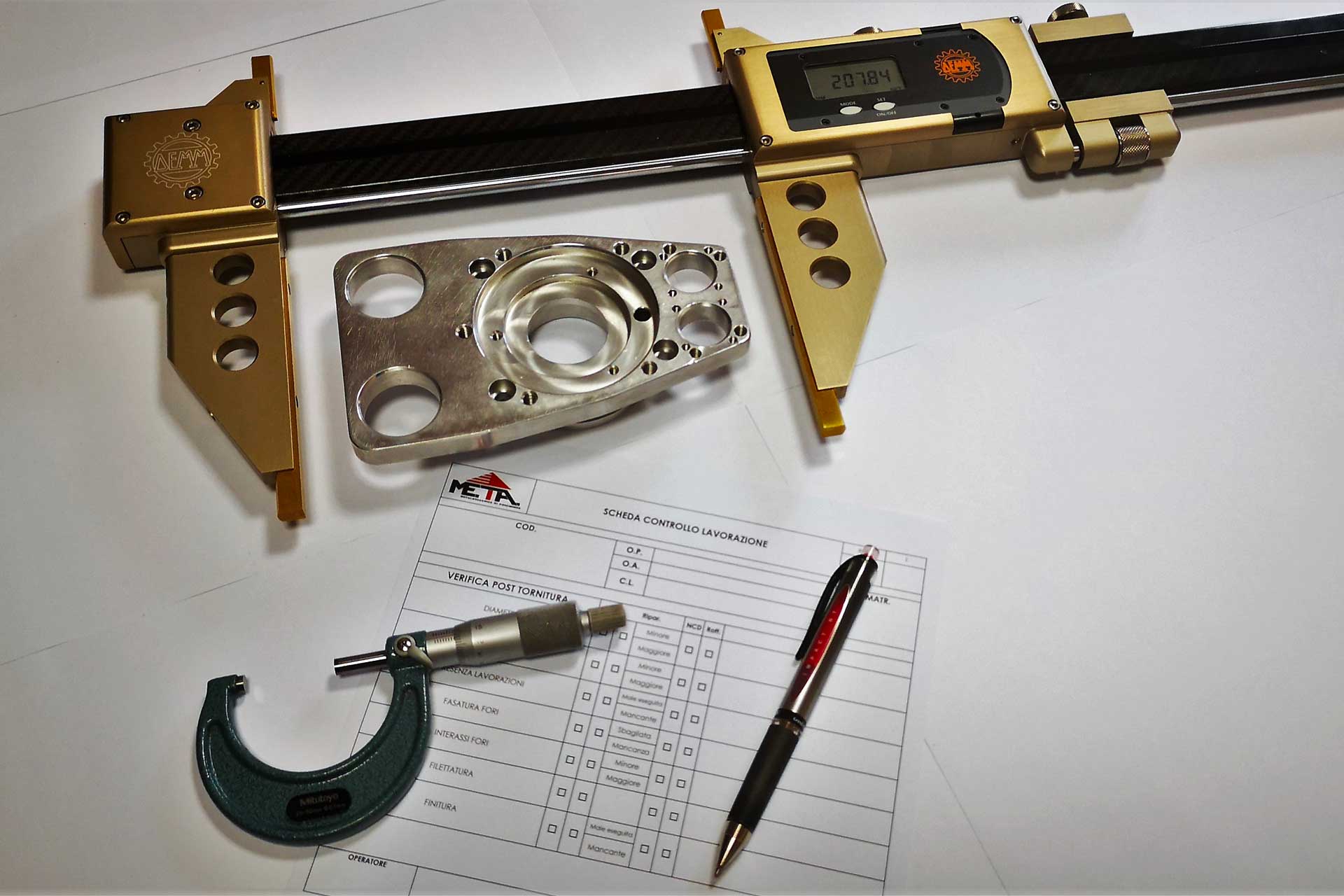
Il collaudo consiste in un controllo dimensionale e visivo di tutti i componenti meccanici che produciamo, viene effettuato durante il processo produttivo ma soprattutto prima della consegna.
Per verificare la conformità o la non conformità dei pezzi rispetto alle richieste del disegno abbiamo a disposizione una vasta scelta di strumenti di misura.
Nello specifico sono:
- Calibri a corsoio fino a mm 1000
- Calibri digitali fino a mm 1500
- Micrometri per esterni fino a mm 700
- Micrometri per interni a 3punte fino a mm300
- Micrometri per interni ad aste fino a mm 1300
- Tamponi lisci fino a mm ø60
- Tamponi filettati passa/nonpassa a profilo triangolare e trapezoidale
- Blocchetti di riscontro fino a mm 30
- Rapportatori angolari